
ININ Research & Design Project Expo
Join us for the ININ Research and Design Project Expo, an inspiring event highlighting the innovation, creativity, and impact of Industrial Engineering students at UPRM. During this showcase, students involved in research, special projects, and senior capstone design will present their work through engaging poster sessions. This is a unique opportunity to explore diverse topics, connect with student researchers, and celebrate the forward-thinking solutions being developed within our department. Come support our talented ININ students as they share their ideas, insights, and contributions to the field.
ININ Research Projects
The ININ Research Projects showcase the innovative work of Industrial Engineering students as they tackle real-world challenges through research. Guided by faculty mentors — Dr. Samuel Bonet, Dr. Betzabé Rodríguez, Dr. Héctor Carlo, Dr. Mauricio Cabrera, and Dr. Wandaliz Torres — students explore impactful topics and apply analytical skills to advance the field of Industrial Engineering.
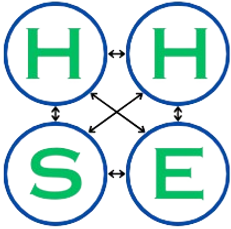
Mentor:
Dr. Samuel Bonet Olivencia
Undergraduate Researchers:
Fabiola A. Acevedo Andino
Ricardo D. Marrero Lugo
Jeriel Sáez González
​
Social Media:
Poster Location: 39
01
Bridging Healthcare Access Gaps: Assessing Telehealth Readiness and Barriers
This study explores Puerto Rico’s readiness for telehealth adoption, assessing attitudes, preparedness, and barriers to technology acceptance in healthcare. It examines both enabling and limiting factors, classifying them by what they measure, such as quality of communication, trust in technology, adaptability, and security concerns. The survey evaluates key aspects like perceived ease of use, anticipated benefits, digital access, and prior telehealth experiences to develop a comprehensive readiness profile. By identifying opportunities and obstacles, this research provides insights for healthcare providers and policymakers to enhance telehealth accessibility, address digital disparities, and strengthen trust in virtual healthcare solutions. Understanding these factors will help bridge gaps in healthcare services, improve patient engagement, and promote equitable telehealth adoption across Puerto Rico. The findings contribute to shaping strategies that ensure effective integration of telehealth, fostering a more inclusive and technologically advanced healthcare system.
02
Manufacturing Framework for STC as a Predictive Tool
Accurate throughput predictions are essential for production control and strategic decision-making in manufacturing. This research evaluates Statistical Throughput Control (STC) as a predictive tool for assessing production target achievement. Through simulation-based analysis, we aim to identify manufacturing frameworks where STC provides reliable insights.
The study's first phase focuses on defining key scenarios, considering factors like production flow, bottlenecks, machine reliability, and workforce allocation. Once established, the next phase will train the predictor to move beyond forecasting, enabling it to provide data-driven recommendations, such as adjusting capacity or scheduling overtime.
Currently in its early stages, this research seeks to integrate predictive analytics with decision-making support to optimize operations. Future work will refine the model to ensure its effectiveness as a practical tool for improving manufacturing efficiency.
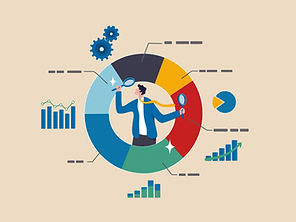
Mentor:
Dr. Betzabé Rodríguez Álamo
Undergraduate Researchers:
Verónica M. Cartagena Lebrón
Crislean M. Olivencia Rodríguez​
Poster Location: 34
03

Mentor:
Dr. Samuel Bonet Olivencia
Undergraduate Researcher:
Sebastian J. Cabán Rodríguez
​
Social Media:
Poster Location: 36
Digital Technologies to Support College Students with ADHD and/or Learning Disabilities
This research project, led by the Human & Health Systems Engineering (HHSE) Lab and directed by Dr. Samuel A. Bonet Olivencia, focuses on addressing the needs of university students in Puerto Rico facing challenges associated with ADHD and/or learning disabilities. After an extensive literature review, multiple existing digital applications were identified that offer support in areas such as organization, task management, education, health, and productivity. However, the lack of concrete evidence on the effectiveness of these tools highlights the need for a more innovative approach. Therefore, the project has evolved toward the development of digital interventions designed to demonstrate the efficacy of these technologies in improving students' quality of life and academic performance. A commitment to engaging all stakeholders remains key, seeking a meaningful and lasting impact that benefits the entire educational community.
04
Towards An Individual Decision-Making Framework to Achieve Mitigation of Climate Change Effects with a Local Perspective​
Natural disasters in Puerto Rico are becoming more frequent and severe due to climate change. This work focuses on the purposeful selection of plants and trees to surround houses to potentially decrease the harmful effects of phenomena like wind, wildfires, floods, plagues and high temperatures. To this end, initial observations from four locations across the island allowed to recognize the function that certain plant characteristics and their environment fulfill in helping them survive and provide protection. Leaf shape, crown shape, type of stem body, among many others, can be used to characterize plant types and assess their level of protection against different phenomena. This step is the first one towards building a decision-making framework where the proposed plant selection and assessment can be carried out by individuals on the island.
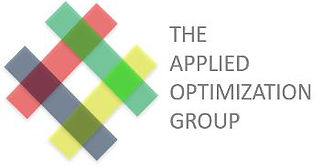
Mentor:
Dr. Mauricio Cabrera
Undergraduate Researchers:
Emmanuel I. Nazario Acevedo
Antonio Monge Perloni​
Poster Location: 41
05

Mentor:
Dr. Samuel Bonet Olivencia
Undergraduate Researchers:
Yamieleny M. Meléndez Ramos​
Valerie N. Morales Rodríguez
Alondra A. Collazo García
​
Social Media:
Poster Location: 40
Modalities in College Education
This study aims to develop a framework to guide institutions in the implementation of online education programs. The main focus is to facilitate a comparative analysis between the current educational infrastructure and identified best practices, considering key elements such as technology, faculty, institution, students, and learning modalities. The methodology included a literature review as well as the development of a questionnaire for students at the University of Puerto Rico at Mayagüez. The questionnaire incorporated questions about students' perceptions of online classes and the driving and inhibiting factors in the use of technology applied to education. The components of the educational system and their interactions were also identified to understand how they influence the effectiveness of online education. This phase will serve as the basis for interviews with faculty members, as well as a deeper analysis of the relationships among these components.
06
Stochastic Capacitated Discrete Facility Location Problem for Energy-Resilience Hubs
Energy-resilience hubs (ERH) are facilities designed to support communities in case of major disruptions by offering services such as device charging stations, power for life-support equipment, and refrigeration for vital supplies. ERHs serve as distribution points for emergency supply goods, hosting emergency operations and command centers. Under routine conditions, ERH could serve as community centers that may host tutoring services, health fairs, etc. This study presents a two-phase linear stochastic discrete capacitated facility location problem for ERH pre-disaster planning to minimize a social disutility function under the assumption that capacity is linear and continuous. The first phase determines the facility location and energy capacity under a budget constraint. The second phase minimizes a weighted disutility function that is directly related to the distance from each community to the facility and the forecasted ERH demand considering multiple disaster scenarios. A Genetic Algorithm (GA) is presented and compared to the optimal results from the exhaustive stochastic formulation using real data from rural communities in Puerto Rico.
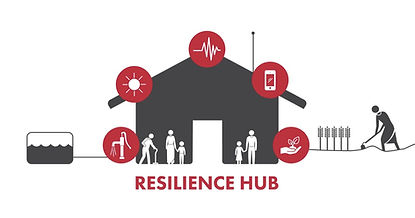
Mentor:
Dr. Héctor Carlo Colón
Undergraduate Researcher:
Abdiel Ocaña Colón
Poster Location: 38​
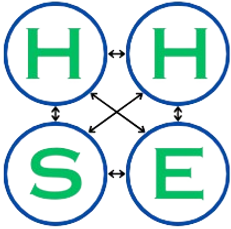
Mentor:
Dr. Samuel Bonet Olivencia
Undergraduate Researchers:
Jossmarie Santiago Burgos
Adriana V. Vázquez Cuevas​
Sara M. Soto Rivera
Emmanuel A. Aleman Alicea
Social Media:
Poster Location: 35
07
Improving Workplace for Safety: Developing an Effective Ergonomics Training Sociotechnical Framework for Puerto Rico
Evolving workplace conditions and changes in the anthropometric profile of the workforce highlight the need for a modernized approach to occupational ergonomics. This research aims to develop an effective ergonomics training framework tailored to the specific needs of local industries. The study adopts a dual approach: first, it assesses the effectiveness of current ergonomics training programs across various industrial sectors, focusing on their impact on employee safety, health, and productivity; second, it addresses the outdated anthropometric data used in the design of workstations and industrial equipment, as the last measurements were taken more than 26 years ago. By collecting new anthropometric measurements from a representative sample of the workforce and analyzing employee feedback on ergonomics training, this study will provide critical insights into the need for enhanced training programs and updated design standards. The findings will help create a standardized framework for ergonomics training, ensuring it meets the contemporary needs of the workforce. This research will ultimately contribute to improving workplace health, safety, and efficiency by aligning ergonomics practices with both current physical characteristics and emerging industry demands.
08
Consensus-Based Hybrid Ensemble Feature Selection Algorithm for Endometriosis Diagnostic Biomarker Discovery
Endometriosis is a disease characterized by the growth of endometrial tissue outside of the uterus. It is known to cause pelvic pain and has been linked with infertility. The diagnosis of endometriosis takes years, partly because the gold standard to diagnosis is a laparoscopic surgery. Previous research to identify potential molecular biomarkers face statistical and computational limitations due to small sample size and high dimensionality. Additionally, there is no standardization regarding factors that may alter gene expressions of endometrial tissue, such as the menstrual cycle. Therefore, we propose the development of a consensus framework to extract the best feature subsets to discriminate between endometriosis patients and non-endometriosis patients using gene expression while considering the menstrual cycle. We aim to identify feature subsets using (1) optimization-based search algorithms coupled with classification methods and (2) queries of functional processes from gene-annotated databases across multiple publicly available experiments from the Gene Expression Omnibus.

Mentor:
Dr. Wandaliz Torres García
Graduate Researcher:
Carolina Arroyo Roldán​
Poster Location: 33
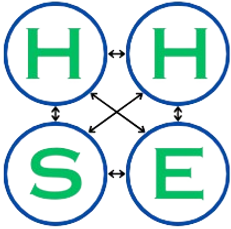
Mentor:
Dr. Samuel Bonet Olivencia
Undergraduate Researchers:
Xamarys Ignacio Menéndez
Yaniel E. Cruz Santa
Iván A. Carrión Ortíz
​
Social Media:
Poster Location: 37
09
Informal Caregivers’ Perspectives: Shaping an mHealth Solution for Dementia Care
Alzheimer’s disease and related dementias (ADRD) affect both patients and their caregivers, who often face stress, burnout, and a heavy emotional and physical burden. In Puerto Rico, ADRD is the fourth leading cause of death, with over 116,000 cases, leaving many informal caregivers—mostly family members—struggling with a lack of support and resources. Mobile health (mHealth) interventions offer scalable tools to empower caregivers by improving their knowledge, coping mechanisms, and care coordination. In this first phase of the study, semi-structured interviews were conducted with 15 informal caregivers of ADRD patients in Puerto Rico, with the goal of identifying key areas where an mHealth intervention, integrated with artificial intelligence, could support informal caregivers both in providing care and in caring for themselves.
ININ Design Projects
The ININ Design Projects represent the culmination of Industrial Engineering students' academic journeys. In these projects, students collaborate directly with industry organizations to solve real-world challenges. Under the guidance of Dr. Lourdes Medina and Dr. Pedro Resto, students work in teams to design and implement innovative, data-driven solutions for companies across various sectors. These projects provide hands-on experience and showcase the value Industrial Engineers bring to today’s industries.
01
Improving Operational Efficiency Through Flexible Workforce Strategy
The Flexible Workforce Strategy project in the Parenteral Manufacturing Area strives to improve production efficiency by reducing excessive overtime and improving workforce adaptability. With a targeted 41% reduction in overtime and ensuring that 44% of operators are cross-trained by the second quarter of 2025, this initiative introduces a structured cross-training program and a robust capacity analysis. By equipping employees with versatile skill sets, the project optimizes workforce utilization, alleviates the strain of high overtime demands, and fosters career growth. A key component of this effort is the development of an interactive dashboard to track overtime metrics, workforce certifications, and capacity insights, enabling data-driven decision-making and strategic workforce planning. Additionally, the initiative supports employee retention and workplace satisfaction by promoting career advancement opportunities. Expected outcomes include increased operational agility, a more resilient workforce, and improved overall efficiency, ensuring long-term sustainability within the Parenteral Manufacturing Area.
Professor:
Dr. Pedro Resto
Undergraduate Students:
Alondra I. Mendoza Ortíz
Alondra M. Trabal Bobé
Poster Location: 18
02
Digitalization Unit Transformation
The Digitalization unit, has not undergone a thorough process evaluation for optimization and standardization. This lack of evaluation has led to limited visibility of their productivity as well as inefficiencies, including duplicated processes and a high reliance on manual operations, which adversely affect processing time, storage/server utilization, and employee wellbeing. To address these issues, it is essential to systematically assess current workflows to identify and eliminate process duplications, explore automation opportunities, and determine the optimal team capacity and staffing requirements needed to effectively manage all tasks.
Professor:
Dr. Lourdes Medina
Undergraduate Students:
Elena V. Vargas Álvarez
David D. Sánchez Félix
Poster Location: 24
03
Implementation of a Production Performance Advisor Application
The organization aims to enhance manufacturing performance monitoring by implementing the Production Performance Advisor (PPA) application across all manufacturing lines and rooms. Currently, performance tracking relies on fragmented data sources and manual inputs, leading to inefficiencies, delayed decision-making, and limited real-time visibility into equipment utilization and production performance.
The project will be executed in phases. Phase 1 focuses on a pilot implementation in Line 6 and Fette 6, where sensors are already connected to the data historian. Phase 2 involves identifying additional lines and rooms integrated with the data historian and extending the PPA implementation accordingly.
Professor:
Dr. Pedro Resto
Undergraduate Students:
Marcos Dávila Velázquez
Raúl A. Peña Muñíz
Poster Location: 27
04
Analysis of Customer Complaints leading to Explainable Causes
The organization aims to enhance manufacturing performance monitoring by implementing the Production Performance Throughout the most recent years, customer complaints have increased regarding a specific product line. These complaints are sporadic but consistent meaning that a small percentage of production is being received defective by customers and is therefore increasing operating costs. Through analysis of production and packaging data we intend to arrive at the root or roots of the problem and correct any assignable causes we might find.
Professor:
Dr. Lourdes Medina
Undergraduate Students:
Diego F. Rivera Hernández
David A. Villahermosa Marrero
Poster Location: 20
05
Safety Switches 30-200 Amp Production Line Pilot Release
Arecibo is developing a duplicate line of the SS 30-200 Amp based on lines running in Monterrey MX. Arecibo needs to integrate the line into it’s operations complying with the QWins Standards in order to be able to runa it’s Pilot and Final Validation.
Professor:
Dr. Pedro Resto
Undergraduate Students:
Rosa M. Laureano Marrero
Carlos A. Padilla Rivera
Poster Location: 31
06
Reducing Packaging Rework in the BT Line at Sartorius Stedim Using a Data-Driven DMAIC Approach
This project aims to reduce packaging-related rework in the Bottle Top (BT) line at Sartorius Stedim, Yauco, where such events currently represent 25% of all rework incidents. Using the DMAIC methodology, historical data from QA and manufacturing reports are being analyzed through control charts, trend analysis, and inferential statistics to identify high-impact root causes, such as mislabeling and packaging inconsistencies. A Work Sampling study complements this effort by assessing operator-related factors and process conditions contributing to errors. Proposed improvements will be evaluated for their operational feasibility and cost-effectiveness using engineering economics tools. The final goal is to decrease packaging-related rework to 12%, enhance process reliability, and support Sartorius’s goals in quality compliance and productivity.
Professor:
Dr. Lourdes Medina
Undergraduate Students:
Luis R. López Ortíz
Freddy A. Justiniano Monserrat
Poster Location: 3
07
Improving Café Oro's Operations through the Application of Basic Industrial Engineering Concepts
This project, part of ININ 4079, focused on improving the operations of Café Oro de Puerto Rico by applying industrial engineering principles in a practical setting. Through collaboration with the owner, key issues were identified, such as machine uptime and downtime, the feasibility of changing packaging reels, production capacity, equipment ergonomics, and production layout optimization. The main objective was to optimize efficiency in the coffee roasting, grinding, and packaging processes. Using Work Systems Design, Time Study, Operations Research, and Cost Management tools, the company recommended a transition to ergonomic equipment, identification of downtime causes, capacity analysis, and a return to the previous, more cost-effective and efficient packaging format.
Professor:
Dr. Pedro Resto
Undergraduate Students:
Elvin G. Ramos Valentín
Abdiel Ocaña Colón
Poster Location: 14
08
Improving Documentation and Reducing Rework Due to Assembly Process Defects in BT Manufacturing
This project aims to reduce assembly-related rework and improve documentation within a manual production area where 10 operators assemble various products across three stations. Each product is composed of OPs (subcomponents) that are manually assembled by operators. The team leader verifies only the first unit each operator assembles; after that, no further inspection is performed at the OP level. Defects are only documented if detected by the Quality department, which inspects the final product once all OPs are combined. In 2024, a 0.192% rework rate was recorded, but this likely underrepresents the actual rate due to undocumented in-station corrections. The objective is to improve rework documentation by 10% and increase inspection rates by 5%. First, current data was analyzed, then the existing documentation process was reviewed. Work sampling was conducted to identify key variables and support targeted recommendations. Statistical analysis, time studies, and cost evaluations will guide improvements in process efficiency, documentation, and rework reduction.
Professor:
Dr. Lourdes Medina
Undergraduate Students:
Rodnny J. Hernández Valentín
Victoria M. Suárez Rivera
Poster Location: 7
09
Flocking Waste Reduction
This capstone project focuses on tackling productivity challenges and identifying scrap reduction opportunities within the Flocking area, using Lean Manufacturing principles to identify inefficiencies, and propose data-driven improvements. The objective is to have a 10% increase in shift run rates—from 60.5K to 67K—and achieve and maintain consistent performance with a 90% reliability or higher. Through tools such as waste analysis, work measurement, and process mapping strategies like spaghetti diagrams, the project can identify areas of opportunity. Updated Standard Operating Procedures (SOPs) and targeted training strategies are proposed to support long-term improvements. Run rate data and employee input help to create better solutions that should be aligned with the company’s goal of reducing waste and optimizing processes.
Professor:
Dr. Pedro Resto
Undergraduate Students:
Ángel G. Corchado Rivera
Xamarys Ignacio Menéndez
Poster Location: 13
10
Increased Subassembly Capacity
This project aimed to identify strategies for increasing the capacity of specific products. To achieve this, a direct time study, a production analysis, and a cost analysis were conducted to assess bottlenecks.
The findings will be presented in a poster, showing what was involved in achieving the project, with general information to maintain company privacy. I also want to add knowledge acquired throughout the project to the capstone.
Professor:
Dr. Lourdes Medina
Undergraduate Student:
Ricardo Acosta González
Poster Location: 2
11
UTM and Eswab Kits Waste Reduction Capstone Project at COPAN Industries, Inc.
Collimatic Eswabs and UTM kits production is currently facing inefficiencies, leading to waste, higher costs, and reduced productivity. Issues such as excess inventory, overproduction, unnecessary movements, and defects are hindering throughput, increasing lead times, and compromising product quality. To address these challenges, the company plans to implement Lean Manufacturing principles to optimize operations, reduce waste, and improve productivity and quality. The goal is to achieve measurable improvements in efficiency, lower costs, and enhance product quality, ultimately boosting competitiveness and profitability.
Professor:
Dr. Pedro Resto
Undergraduate Students:
Veronica D. Borrás Serrano
Fernando A. Soto Torruella
Poster Location: 23
12
Deployment for Extraction Hood in the Cartridge Area
This project, carried out in collaboration with Johnson & Johnson Medtech in Añasco, Puerto Rico, aims to evaluate deployment alternatives for integrating a fume hood in the Cartridges area, in order to reduce exposure to isopropyl alcohol to 70%. The analysis is carried out through three modules: Work Systems Design and Motion and Time Study, Plant Design and Layout, and Engineering Economics and Managerial and Cost Accounting. Three proposals are developed and evaluated using tools such as work sampling, spaghetti diagrams, and cost analysis, seeking to improve occupational safety and operational efficiency without affecting workflow.
Professor:
Dr. Lourdes Medina
Undergraduate Students:
Ana B. Delgado Robles
Adriana M. Berríos Matos
Poster Location: 9
13
TEY 2/3 Poles KPI Improvement
The TEY 2/3 Poles Production Line, the second-highest revenue-generating line, is facing inefficiencies that are affecting key performance indicators (KPIs). Currently, the first pass yield (FPY) stands at 83%, with a target of 85%, and there is an additional goal to reduce rework costs by 4%. Success will be measured by achieving tangible improvements in the identified KPIs: FPY, rework costs, and labor productivity.
Professor:
Dr. Pedro Resto
Undergraduate Students:
Adriana P. Baez Guzmán
Alondra V. Luna Ramírez
Poster Location: 8
14
Improving Production Efficiency and Inventory Management at MOM
Mayagüez Optical Manufacturing (MOM) is currently facing operational challenges related to uneven operator workload distribution, inventory control issues, and workplace disorganization, factors that contribute to prolonged production cycles and elevated costs. This project applies industrial engineering methodologies such as line balancing, a Kanban-based inventory system, and 5S principles to enhance workflow efficiency and reduce waste. Through the DMAIC framework, process inefficiencies are identified and analyzed using time studies and capacity analysis, enabling data driven decision making. The proposed strategies aim to streamline operations by improving inventory responsiveness to demand, enhancing workplace organization, and minimizing idle time across production stages. By reinforcing ergonomic practices and aligning resources more effectively, MOM is positioned to achieve sustained improvements in efficiency, productivity, and competitiveness within the optical manufacturing sector.
Professor:
Dr. Lourdes Medina
Undergraduate Students:
Paola C. Cabrera Morales
Alondra A. Collazo García
Poster Location: 15
15
Reducing Financial Statement Close Time to Seven (7) Days
This project aims to streamline Premier Insurance and Premier Warranty's financial closing process, reducing time while ensuring accuracy and compliance with accounting standards.
Professor:
Dr. Pedro Resto
Undergraduate Students:
Andrea L. García Guadalupe
Natalia M. Rodríguez Nieves
Poster Location: 6
16
Universal Relay Order Picking Optimization
This project for GE Vernova in Añasco focuses on optimizing the material picking process for the Universal Relay product. Inefficiencies were found in the time and accuracy of the order preparation process, which impact operational efficiency and order fulfillment effectiveness. The main objective is to increase the efficiency and accuracy of material picking by 5-10% through recommendations regarding optimizations in warehouse deployment or available space, process standardization, and the application of Poka-Yoke techniques to minimize errors. To this end, work studies, deployment analyses, and economic evaluations were conducted to determine the feasibility of the proposed suggestions. These recommendations will be validated through theoretical tests with a focus on generating a positive impact on line productivity and capacity.
Professor:
Dr. Lourdes Medina
Undergraduate Students:
Esthefanie N. Marrero Figueroa
Karelys Pérez Santiago
Poster Location: 19
17
COPAN Industries - Filling Area
This project aims to improve the production capacity of COPAN Industries' filling lines, increasing production from 23,000 to 26,000 units for UTM and similarly from 30,000 to 35,000 units for Eswab. Key issues identified include downtime resulting from a shortage of maintenance technicians, as well as inefficiencies during shift changes, where both incoming and outgoing technicians spend significant time cleaning machines. Through a thorough process analysis, the company seeks to optimize resource use, minimize downtime, and improve operational efficiency. Preliminary results indicate that restructuring technician scheduling and improving cleaning procedures during shift changes are crucial to achieving the desired production increase and reaching the target of 26,000 and 35,000 units.
Professor:
Dr. Pedro Resto
Undergraduate Students:
Alexis J. Fuentes Huertas
Yillian M. Alicea Cardona
Poster Location: 26
18
Layout and Work Measurement Control in a Production Plant
This project seeks to implement all the knowledge and tools acquired throughout high school. It is designed to give students their first taste of the workforce. In our case, the project is aimed at a Puerto Rican pitorro distillery. All necessary improvements will be sought to ensure the company can meet demand at the lowest cost and achieve the profits and goals established by the company.
Professor:
Dr. Lourdes Medina
Undergraduate Students:
Migdaliz M. Lisboa Mercado
Dayanyadi N. Trabal Vargas
Poster Location: 28
19
AI Demo Resiliency
Live demos are a fundamental part of selling any product to a customer. These demos working as they should when presenting is what set them apart from external competition. After a series of investigations and interviews, we aim to gather enough data to make a definitive analysis as to why these demos fail during live presentations. This analysis focuses on three primary demo failures which are: Environmental Factors, Technical Malfunctions, and AI Issues. Environmental Factors such as team coordination or connectivity issues. Technical Malfunctions within the demo that does not allow the demo to continue with the flow that was intended. While AI Issues, behave unpredictably or goes off the intended script. By understanding these failures, we can implement targeted solutions to avoid failures from re-occurring and prevent revenue loss.
Professor:
Dr. Pedro Resto
Undergraduate Students:
Brianna S. Duggal Santiago
Pedro A. Bilbao Rosa
Poster Location: 5
20
Alyx Capacity Increase
The Alyx Cell production line at Fresenius Kabi is facing a bottleneck in the robot module, limiting capacity to 33 units per hour and impacting operational efficiency. This project seeks to optimize workflow by implementing a second robot and redistributing tasks. Time studies, capacity analyses, and financial evaluations will be conducted to ensure an efficient balance between stations. The expected results are increased productivity, reduced downtime, and improved process profitability.
Professor:
Dr. Lourdes Medina
Undergraduate Students:
Rashell M. López Díaz
Alvin E. Saunders Altreche
Poster Location: 21
21
Abbott Vascular: Optimizing Handsewing Process
At Abbott Vascular, Master and Regent heart valve replacements are manufactured through mostly manual processes. The handsewing production line is the process bottleneck and consists of Tissue Anulus (TA) and Flange workstations. Improvement opportunities were identified in order to address high process variability, process wastes and production workflow. This, resulting on reduced cycle times, increased production capacity and efficiency (UPPH).
Professor:
Dr. Pedro Resto
Undergraduate Students:
Yarelis A. Hernández Hernández
Angel L. Ruiz Fernández
Poster Location: 22
22
Increasing Subassembly Capacity to Support Production Demand
This project focuses on evaluating and improving the production capacity of two critical subassemblies, A and B, at Fresenius Kabi’s San Germán facility. Subassembly A consists of two production lines, while Subassembly B operates on one line. A time study was conducted across 14 manual and semi-automated workstations to establish standard times, identify inefficiencies, and model baseline capacities. Observations included occurrences of rework, scrap, and operational delays. The objective is to increase the output of these subassemblies through phased improvements of 300 units per shift, reaching up to 900 additional units per shift. Work system analysis, capacity analysis, and economic evaluation methodologies were applied to assess current operations and develop scalable improvement strategies.
Professor:
Dr. Lourdes Medina
Undergraduate Student:
Kimberlie C. López Pabón
Poster Location: 4
23
Minimizing PMG's DTM: Analysis & Optimization of Existing Processes
Currently, the Collins Aerospace Santa Isabel site does not have an established method to determine the required number of operators per manufacturing cell, including the PMG cell in PR-6 building. In 2024, given the site’s high-mix, low-volume nature, the cycle time (DTM) for the PMG cell was approximately 15 days (on average). This project aims to analyze the PMG cell using operations research, line balancing, and a current-state simulation to determine the required number of operators and improve overall efficiency. It will also serve as preliminary groundwork toward simulating other manufacturing cells within ePRO to improve resource allocation and support better decision-making. The success metric for this initiative is to reduce the cycle time by 30% compared to the 2024 baseline, lowering it from 15 days to 11 days.
Professor:
Dr. Pedro Resto
Undergraduate Students:
Yeiza A. Báez Santiago
Cristina M. Bonilla Cruz
Poster Location: 12
24
Capability & Capacity Analysis for PCA's Manufacturing Repair Operations
This project aims to analyze and improve repair operations at PCA manufacturing, focusing on three local production lines operating on two shifts. One of these lines is dedicated to New Product Introduction (NPI), which requires the engineering team to create new recipes when units fail, increasing process time. Additionally, the project will address customer return management.
The goal is to conduct a comprehensive capacity and performance analysis, using historical SharePoint data (Repair Tracker) to develop a new metric that correlates repair time with repair type.
Professor:
Dr. Lourdes Medina
Undergraduate Students:
Dariel G. Pérez Durán
Erwin F. Alequín Pérez
Poster Location: 10
25
100cc Reservoir Assembly Automation
This project aims to automate the assembly and inspection process for Cardinal Health's 100cc Reservoir to improve operational efficiency, reduce labor costs, and increase production capacity. Following previous studies focused on time analysis and automation, the current phase (January–May 2025) focuses on designing an automated system to feed, assemble, and inspect the 100cc reservoir with minimal human intervention. The proposed solution includes collaboration with local suppliers for the acquisition of the necessary equipment and software. Key objectives include reducing labor by more than 80%, minimizing product rejection, and achieving a favorable return on investment (ROI). The methodology includes layout redesign, time studies, and economic analysis to support investment decisions. The project is expected to improve product quality and strengthen the company's competitiveness.
Professor:
Dr. Pedro Resto
Undergraduate Students:
Edward J. Cruz Vega
Keishlyan Ramos Bauzá
Poster Location: 11
26
Separation Technology (ST): Raw Material Transaction Flow and Control
At Sartorius’ Yauco site, the Separation Technology (ST) business unit identified raw material inventory discrepancies totaling $119K, representing 35% of the ST inventory, during the physical inventory conducted in December 2024. These discrepancies between SAP system records and actual inventory levels negatively impact material flow visibility, leading to shortages, production delays, and financial losses. Using the DMAIC methodology, the assessment revealed that the primary root causes were human errors and unconfirmed transactions within the SAP system. The project involved a comprehensive evaluation of process flows, the utilization and tasks of material handlers, and the current inventory system to identify critical control points. Both qualitative and quantitative techniques were employed to gather insights from key stakeholders and systematically identify contributing factors. Through the implementation of targeted strategies, this project aims to enhance material traceability, optimize standard operating procedures, and significantly reduce transaction-related errors.
Professor:
Dr. Lourdes Medina
Undergraduate Students:
Yamieleny M. Meléndez Ramos
Fabiola A. Acevedo Andino
Poster Location: 16
27
Reducing Waste in the Manufacturing of Individually Wrapped Sample Collection Swabs
The project, Reducing Waste in the Manufacturing of Individually Wrapped Sample Collection Swabs, aims to reduce waste and improve efficiency in the production of single-use swabs at Copan Industries in Aguadilla, PR. Currently, shift production is below the 2025 target of 43,000 units. The focus will be on optimizing the operations of machines 248 and 249, two of the three machines furthest behind production goals, through time studies, station layout analysis, and the application of continuous improvement tools. The objective is to consistently reach at least 38,700 units per shift and increase production speed by 10% or more by May 2025. These improvements are expected to reduce costs and increase labor utilization. Additionally, proposed operational changes will take operator feedback into account to ensure sustainable and continuous improvement.
Professor:
Dr. Pedro Resto
Undergraduate Students:
Carolina A. Vargas Rivera
Emmanuel I. Nazario Acevedo
Poster Location: 17
28
Customer-To-Check Pre Check
This project focuses on optimizing the production and management of Customer-To-Order (CTO) products by applying Industrial Engineering methodologies. By standardizing processes and utilizing data-driven decision-making, we aim to enhance efficiency, reduce changeover times, and allocate resources more effectively. Key strategies include refining workflow design, optimizing material planning, and improving production times to meet customer-specific demands with greater precision and agility. The integration of Lean Manufacturing principles minimizes waste, enhances quality control, and supports operational scalability. Additionally, a centralized database will enable real-time tracking of orders, resource allocation, and performance metrics, fostering better materials management and documentation. By combining engineering best practices with advanced data management solutions, this initiative seeks to boost productivity, optimize costs, and improve customer satisfaction. Ultimately, the project will establish a more responsive, agile, and competitive manufacturing process, with the capability to meet dynamic market demands.
Professor:
Dr. Lourdes Medina
Undergraduate Students:
Kiara N. Rivera Sánchez
Shantal Cruz Colón
Poster Location: 1
29
LP01 Flow and Tasks Optimization
The LangenPac LP01 manufacturing process has undergone recent changes, creating opportunities to enhance workflow efficiency, optimize space utilization, and improve ergonomic safety. The goal is to increase Overall Equipment Effectiveness (OEE) in the LangenPac LP01 line from 32.2% to 39.1% by the end of May 2025. The team conducted a detailed analysis of the production process following the DMAIC methodology. Data-driven techniques such as time studies, and workflow analysis were perform to identify root causes and implement sustainable improvements. Inefficiencies in motion, material handling, and workstation layouts were identified as key factors impacting equipment availabily, resulting in a low OEE for the LP01 manufacturing line. Through optimized work systems design and layout improvements, OEE increase by 7% and productivity is enhance by 5%. The project goal, aligns with the company’s key performance index of 39% of OEE and also maintain product quality and encourage a safe manufacturing line.
Professor:
Dr. Pedro Resto
Undergraduate Students:
Alejandra V. Reyes González
Natalia I. Torres Rivera
Poster Location: 25
30
BPPR ACH Unit Transformation
The BPPR Automated Clearing House (ACH) manages electronic transactions for businesses and individuals across Puerto Rico. Two critical areas within ACH—Customer Deceased and Exceptions—have not undergone formal process evaluations, leading to inefficiencies such as excessive manual work, unclear key performance indicators (KPIs), and increased processing times. This capstone project aims to assess current workflows, identify automation opportunities, and enhance resource utilization without compromising process quality. Industrial Engineering tools, including Information Systems Design and Time Studies, are applied to analyze current workflows and determine optimal staffing and resource allocation. Solutions will be guided by BPPR’s BASICS methodology: Baseline, Assess/Analyze, Suggest Solutions, Implement, Check, and Sustain. Automation technologies will be explored to enhance operational efficiency without compromising quality. Finally, Cost Management and Economic Analysis principles will be used to evaluate the financial impact and estimate the project’s return on investment (ROI), supporting a data-driven approach to sustainable process improvement.
Professor:
Dr. Lourdes Medina
Undergraduate Students:
Andrea P. Sepúlveda Vargas
Jadiel A. Martínez Rodríguez
Poster Location: 29
31
Los Teques Process Improvement Project
During this project, we have been working with Los Teques, a Puerto Rican company dedicated to the production of tequeños. Los Teques has a production line consisting of the following stages: dough preparation, dough lamination, filling preparation, tequeño rolling, and final packaging.
Currently, the company faces the challenge of increasing its production to meet growing demand. For this reason, they approached the university to evaluate and analyze current processes and implement improvements to the tequeño assembly and packaging system that would allow for increased production capacity.
This project primarily focuses on three areas: time measurement, deployment design, and economic analysis.
Professor:
Dr. Lourdes Medina
Undergraduate Student:
Guillermo J. González Alsina
Gerardo Ortiz Goitía
Poster Location: 30